Prototype #3
The prototype we are building allows the recognition of the shape of the various pieces entering the spray booth using a camera and Computer Vision algorithms, detecting the shape and calculating the critical points of every single piece, in order to inform the operator to which areas he must pay close attention.
Bearing in mind that the software must be used by an operator in a factory, the information must be easily visible and the interaction must be reduced to the bone. Operators most likely wear gloves and using touchscreens may not work, that’s why we need to keep it simple and functional.
Field research
As we’re working with Tecnolaser, a company based in Padua (Italy), that deals with the cutting, bending and painting of metal parts we’ve decided to start with field research.
We conducted field research to understand all the details of how the production line works and how we could optimise the quality and efficiency of their processes, in order to guarantee their customers an excellent final product.

The research has included the following:
Survey of time needed to carry out certain activities
Structured interviews with company managers
Structured interviews with technical people and operators
Observation of the manufacturing processes
Video recording
Thanks to structured interviews with the operators we could highlight the most relevant critical points:
Organising the pieces on the carousel system without consistency in terms of shape and size
The pieces have different shapes and sometimes there are corners which are difficult to reach with the automated painting system
The pieces, ready to be shipped, are associated with their specific pallet only by visual inspection and recognition by the operator.
The quality of the evening work is affected by the fact operators are exhausted, so their work is less precise.
Testing hypothesis and definition of the solution
Thanks to field research and the interviews with experts allow us to identify their main need: understanding their key objects and the automatic detention of the critical areas to be painted (e.g. corners or edges).
In fact, the research has shown that every point on a piece where the paint is not present can be easily attacked by rust in a very short time.
In addition, pieces with errors are treated as waste material.

Specifically, the Object recognition software performed by a camera, sends some useful information to the operator, on a tablet interface.
User Interface Design
The UI design has started fro, the needs of the end-user.
Human-centred design
Human-centred design or people-centred design is a design approach that puts one or more types of people at the centre of the project, identifying them as the main users of a digital product.
People using a digital product are driven by goals and needs.
Designing for them means responding to their motivations and ensuring that they are guided to take the actions that are functional to achieving their goals.

The end-user, in this case, is the paint operator
The paint operator acts to check the quality of the product and to carry out any manual finishing touches. Painting defects or errors are fixed manually by the operator during the process.
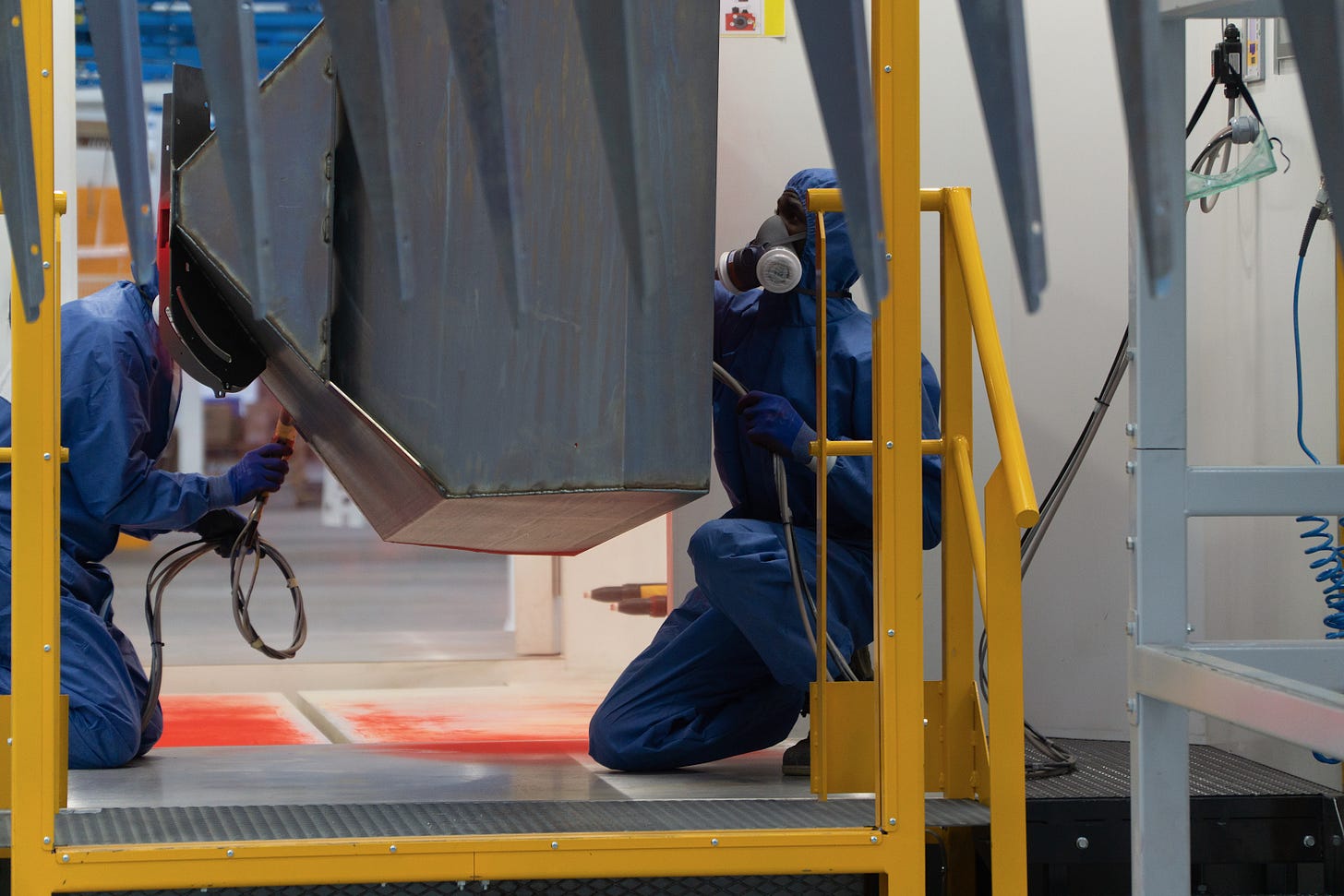
As a first step, we collected the required information for the operator to explain the carousel system and the object he will perform the check.
We have decided to allocate most of the screen space to the object being painted, which turns around automatically highlighting the critical points.
UI is all enclosed in a banner at the top, with the essential information about the serial code, the number of pieces, and the type of job to be done.
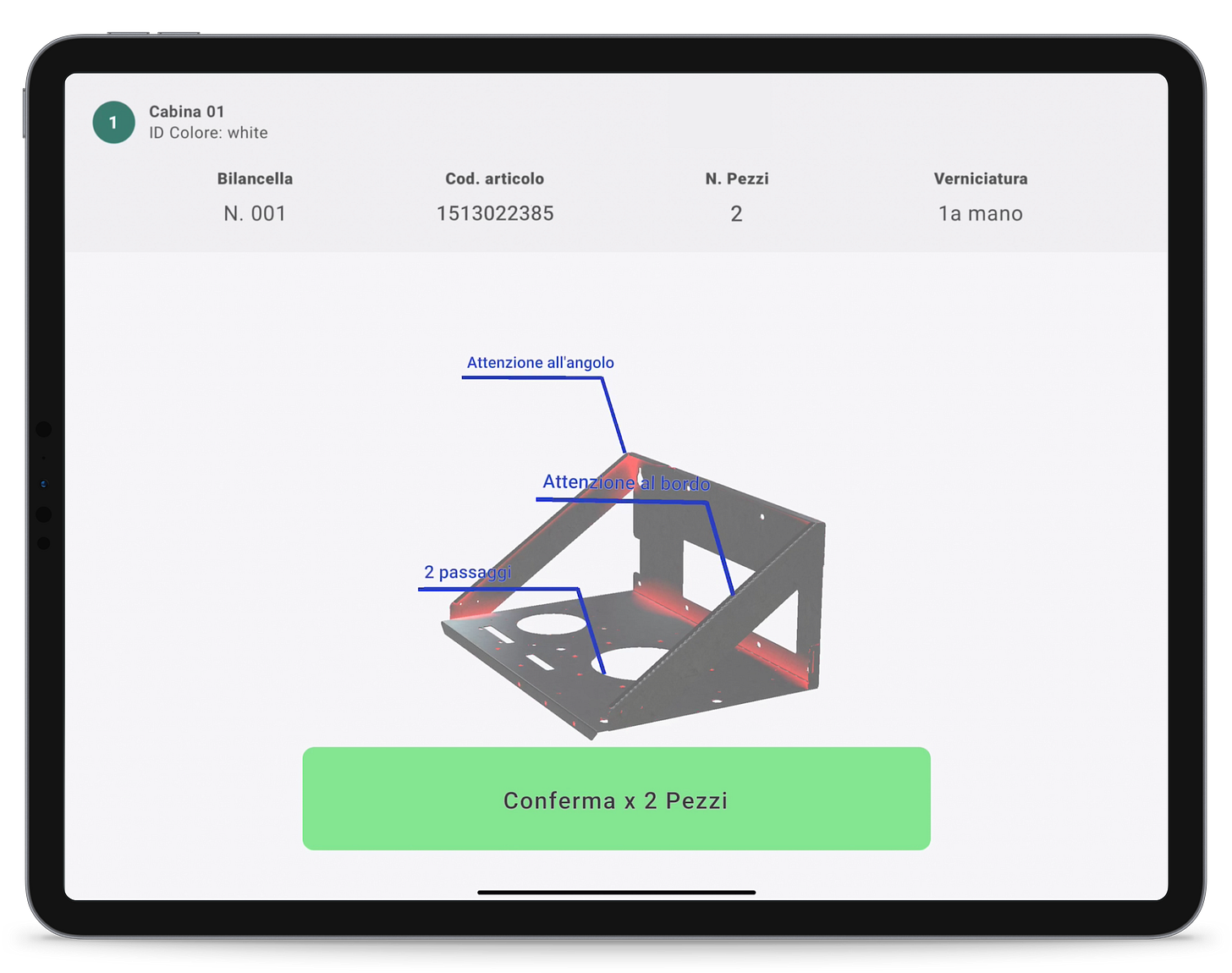
When working in contact with chemicals of different degrees of toxicity, the operator must comply with work safety regulations and those relating to the use of Personal Protective Equipment (such as gloves, masks, protective goggles, overalls).
So, considering the clothing and the type of work, we decided to minimize interactions.
We have therefore designed a UI with a relevant and very visible green Call To Action. To avoid the use of the touchscreen, the tablet also has a series of sensors at the front, to detect the distance of a hand. When the operator gets close, for 5 seconds, positioning the hand on the camera of the tablet, the software proceeds as if the operator has clicked the Call To Action.
Once the Call to Action has been clicked, the software displays the next component to be painted and all the relevant information.
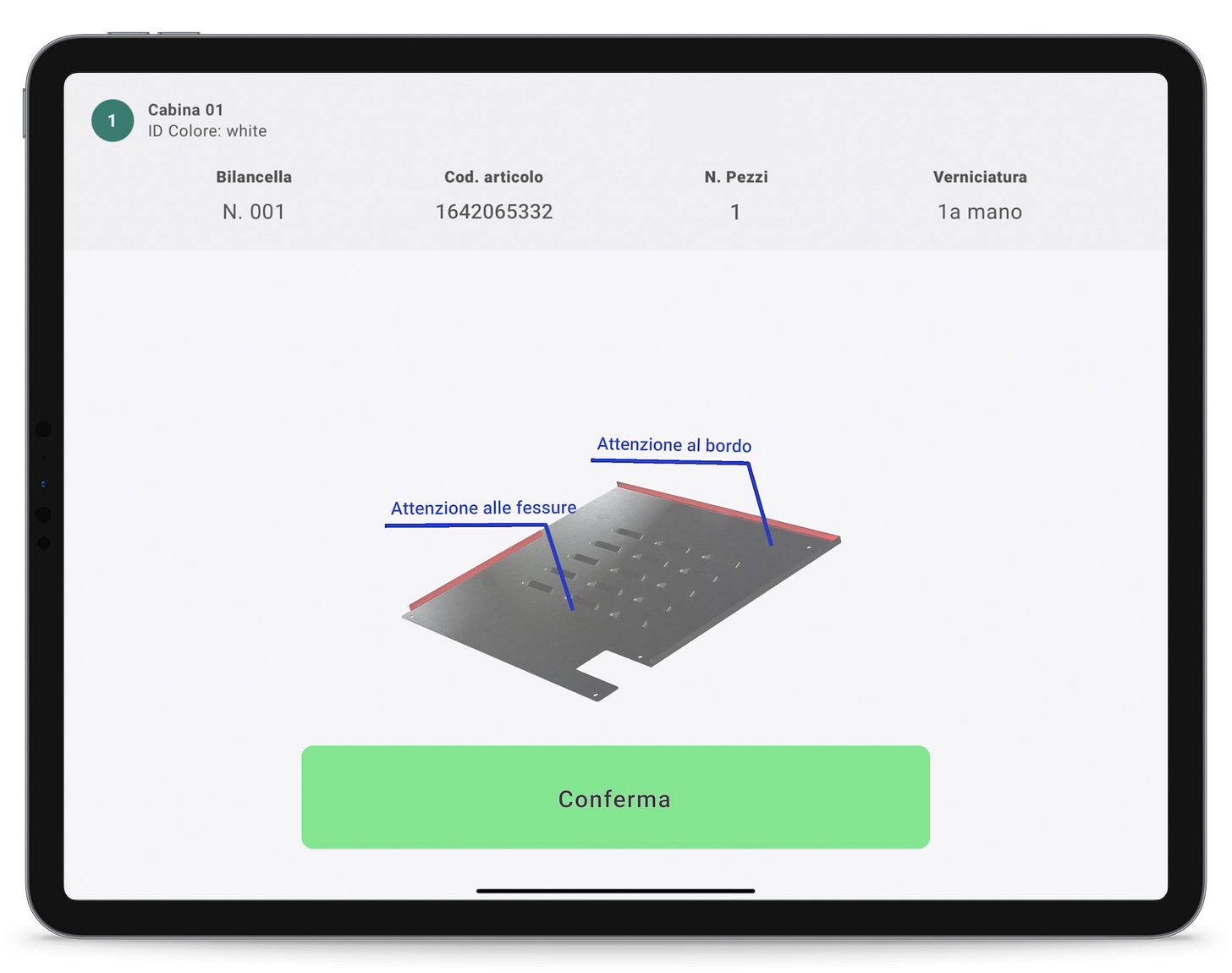
User Testing
Once the first part of the design is completed, it is extremely important to test the output with the end-users.
User testing is an analysis that it’s needed to study the behaviour of a user in relation to the achievement of a goal while using a digital product. It is a test done with a real person watching and browsing the tablet/PC/app in front of a researcher.
Specifically, through a structured interview and direct observation, we analysed the following points:
Usability of the prototype
Clarity of information reported
Color analysis

Conclusion
Doing field research, with the end-users of the digital product, is of fundamental importance throughout the design and testing phase.
It’s allowed us to respond to the real needs of the user, to validate what has been achieved and to iterate the design.